
General Notes on Wiring
This section summarises some
general information I gathered, lessons I learned by experience, and
conventions that I followed when it comes to the
airplane's wiring.
Wire and cable types and sizes
Unshielded wire
Circuits carrying significant
DC current use MIL-W-22759/16 wire, which is the standard aircraft
Tefzel-insulated tin-plated stranded copper wire. It is rated for up
to 150° C and 600 V. For practicality, 18 AWG wire
(MIL-W-22759/16-18) will generally be used for all circuits carrying up to
7.5 A loads, and will be protected by up to a 10 A circuit breaker or other
current-limiting device. For circuits carrying heavier loads, or as
dictated by voltage drop considerations,
heavier-gage wire will be selected as needed.
Shielded wire and cable
Noise-susceptible sense circuits (switch closures, position sensors, etc.)
and noise-inducing circuits carrying alternating currents (PWM servo or
lighting control, etc.) use MIL-C-27500/18 single- or multi-conductor
shielded cable. Note that the individual wires in MIL-C-27500 are
MIL-W-22759. For practicality, 22 AWG wire (MIL-C-27500/18-22) will
generally be used for all circuits carrying up to 3 A loads, and will be
protected by a 5 A circuit breaker or other current-limiting device.
Alternatively, 24 AWG wire (MIL-C-27500/18-24) may be used for circuits
carrying only negligible current. Note that the current-limiting device may be as simple as a series
resistor for some circuits that carry only negligible current.
For multi-conductor cables, the individual conductor insulators are
color-coded according to one of two standards (which is annoying and
potentially confusing... why did they do that?). And for each
standard the colors are either stripes over white, or alternatively just a
solid color (11 through 15 being double stripes over white, or a stripe of
the second color over the first color).
Color coding standard A:
1. white
2. blue
3. orange
4. green
5. red
6. black
7. yellow
8. violet
9. gray
10. brown
11. blue/blue
12. orange/orange
13. green/green
14. red/red
15. black/black
Color coding standard B:
1. red
2. blue
3. yellow
4. green
5. white
6. black
7. brown
8. orange
9. violet
10. gray
11. red/white
12. blue/white
13. yellow/white
14. green/white
15. black/white
Coax cable
Antenna installations will
generally use RG-400,
dual braided-shield, Tefzel-insulated, 50 ohm coaxial
cable. Both RG-400 and RG-142 are in common use in light aircraft these
days, and have superseded the ancient PVC-insulated RG-58. The key
difference between RG-142 and RG-400 is that RG-142 uses a solid core wire
whereas RG-400 uses stranded wire. As a result, RG-142 is favored
for easier connector installation, and RG-400 is favored for cable routing
since it is more flexible and less prone to fatigue damage.
Otherwise, RG-142 and RG-400 can be considered equivalent in their
electrical properties.
I'm standardizing on RG-400.
Connectors
BNC and TNC
BNC (Bayonet Neill-Concelman)
and TNC (Threaded Neill-Concelman) connectors are commonly used for terminating
RF coax
cable. They are used extensively in terminating antenna cables in
general aviation aircraft (VHF comm, nav, ELT, transponder, GPS, etc.
BNC is still more common than TNC, but TNC with its generally better
performance at microwave frequencies is finding more use in newer
avionics, and especially those components operating above 1 GHz (GPS/WAAS,
transponder, ADS-B).
A couple of gotchas to be aware of:
1. BNC connectors come in both 50 ohm and 75 ohm impedence. General
aviation antenna applications are typically 50 ohm impedence.
2. BNC connectors are available for the plethora of different coax cable
standards available. While RG-400 cable has largely replaced RG-58
in new aviation installations, RG-58 can still be commonly found in
aviation as well as non-aviation applications. A subtlty with
connectors is that RG-58 and RG-400 cable are similar enough in their
basic dimensions that connectors designed for RG-58 will typically fit
RG-400 cable well enough, and I've observed that connectors sold by many
aviation sources for RG-400 cable are actually specified by the
manufacturers as being for RG-58, not RG-400 cable. While this seems
to be common and hasn't proven problematic in the field, it seems to me
that using the correct connector would be better practice. And since
connectors specified for RG-400 are readily available and not
significantly more expensive, that is what I intend to use. Note
also that the RG-400 connectors are generally available from the usual
non-aviation sources (Allied Electronics, Digikey, Mouser, Newark, etc.)
at lower prices than the aviation-specific sources.
To keep things simple, I will standardize on the following connectors for
RG-400 cable:
Amphenol / Connex 112514: straight BNC plug
Amphenol / Connex 112526: right angle BNC plug
Amphenol / Connex 112652: bulkhead BNC jack
Amphenol / Connex 122372: straight TNC plug
AMP/Tyco Miniature Circular
Plastic Connector (Miniature CPC)
The AMP/Tyco Miniature
Circular Plastic Connector (Miniature CPC) series are environmentally rugged,
compact, and versatile, making them well suited for wire harness
termination for a majority of airframe functions. These connectors
are available in free-hanging and panel mount varieties, and two shell
sizes: size 8 for up to 4 contacts, and size 11 for up to 9
contacts. They use stamped open-barrel crimp contacts, which are
available for a variety of wire sizes (18 AWG to 30 AWG), and seem to do
well with a generic crimping tool. They are rated for 7A (with 18
AWG wire), which will suffice for all but a few airframe functions.
They are relatively cheap, and readily available from Digikey, Mouser,
etc.
AMP MATE-N-LOK
Notes.
AMP PIDG
Notes.
DB Connectors
Notes.
Wire harness supports
Cusioned clamps (a.k.a.
"Adel" clamps)
Cushioned clamps are used
extensively on production aircraft and are one of the best ways to secure
a wire bundle (or tubing) to a structure where a screw can be used.
They come in a wide variety of diameters, and can be selected to fit wire
bundle snugly. Of the different flavors available, I prefer to use
the MS21919-WDG series clamps, which have a "wedge" at the
opening that helps maintain a circular shape to the inside of the clamp
and therefore spread the loads more evenly and not tend to pinch a
corner. The slightly more common and slightly cheaper MS21919-DG
series clamps don't have the wedge but are otherwise identical.
Snap bushings
Van's makes extensive use of
hard plastic "snap bushings". These slip into a hole and
snap into place with no other fasteners or adhesives required. They
then provide a smooth broad low-friction inner surface for the wiring to
run through, thereby preventing chafing of the wires. These come in
a variety of inner and outer diameters, so they can be matched to the wire
bundle fairly closely if planned in advance, but since they are rigid, the
wire bundle should fit somewhat loosely and therefore will have the
freedom to vibrate some inside the snap bushing. These are not
milspec parts and are not generally used in certificated aircraft, but
they seem to work well in the experimental fleet. Heyco is the
common manufacturer for these as sold by Van's, Spruce, etc., although
other similar generic brands of snap bushings do exist.
Wire ties (a.k.a. "zip
ties")
Zip ties are one of the most
versatile inventions of all time, right up there with duct tape.
They can be used to hold a wire bundle together along its length, or to
secure it to a structure with a zip tie base, wrapping it around a
structure, or slipping it through one or two small holes in the
structure. One important caution: do not secure a zip tie around a
structure that is prone to heavy vibration, such as an engine mount.
The zip tie, made of hard nylon, can actually wear through the metal
structure over time.
Found some neat little zip tie bases: HellermannTyton
p/n CTM0, sold by Spruce in bags of 50 as p/n 11-03987, and can also
be found in different quantities through various non-aviation
vendors. These bases are very compact, fairly rugged, and most
uniquely are installed with a hard fastener, not an adhesive pad.
This particular part number has a hold for a #6 screw. And
incidentally, it also works really well with an LP4-3 pop rivet.
Non-rigid conduit
Some folks use split
corrugated plastic conduit for their wiring runs. This can help
against chafing in some situations, although preferably chafing should be
prevented by adequate separation from structures). Conduit can also
make it easier to fish wires through after the fact. But otherwise
it does not offer any significant rigidity that would alleviate the need
for other means of mechanical support for the wiring. I don't see
much harm in using conduit, but a few potential downsides are water
trapping, less air cooling for the wires, reduced access for inspection of
the wires, and the conduit itself has edges that could chafe the
wires. I decided to not use this type of conduit, or any conduit for
the most part (with one exception, see below).
UPDATE: I bought some of Van's conduit to possibly use in the forward
cockpit. Seemed like cheap plastic... so I took a piece and
conducted an unscientific burn test -- put a flame to it and see what
happens. To my surprise it actually stood up to the flame with no
noticeable effect for several seconds. But then it ignited and
burned vigorously. At that point, when I removed the source of the
original flame, the conduit had no inclination to self-extinguish.
Kept on burning, and producing an aweful smelling thick black smoke.
Conclusion: this conduit has no place in my airplane.
Rigid conduit
The aft fuselage lacks any
good means for supporting the wire harness running out to the tail between
bulkheads F-707, F-708, and F-710. There's a distance of approx 2 ft
between bulkheads, which is too far of a span for an unsupported wire
bundle. Some folks attach sticky zip tie bases to the bottom skin
and attach the wiring to that, and some folks drill holes in the
J-stringers and zip-tie the wiring to that, but both seem pretty kludgey
to me. The skin is not strong, and attaching the wire bundle to it
will add stress. I'm also uncomfortable with the idea of perforating
the J-stringers, as well as the potential for the wires to rub on the
edges of the stringers. I decided to take a different approach
entirely and install a rigid conduit that spans the distance for the
wiring to run through. I considered both plastics and metals for the
conduit material, and ultimately decided to use aluminum, being light,
strong, easy to work with, and non-flammable.
I used 5052-0 tubing, 1/2" OD and 0.035" wall thickness for a
0.43" ID, just over 4 ft long and weighing about 4 oz. I passed
it through the existing 0.625" holes in the F-707 and F-708
bulkheads, and fashioned a hole in the F-710 bulkhead that is co-linear
with the other two, so that the tube can remain straight. I then
fitted a bracket to each bulkhead to which the tubing can be fastened with
a cushioned clamp (MS21919-WDG8) such that it is centered in the hole and
cannot touch its sides. As for the ends of the tubing, I carefully
de-burred them and gave them a bit of a "trumpt" shape on the
inside so that the wires won't rub against a sharp edge. I also
slipped some snap bushings over the tubing, which is an unconventional use
of them, but fit perfectly and provides a very benign exit to the
conduit. Ok, too many words, here are some photos:
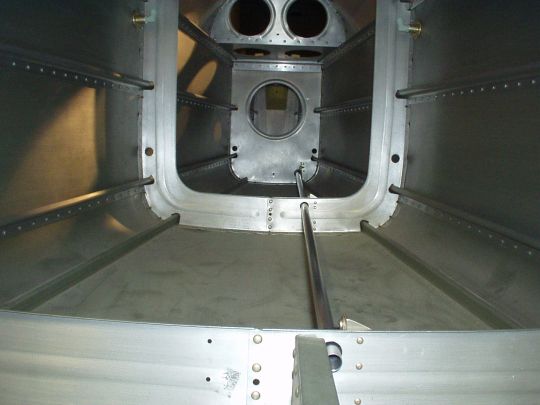
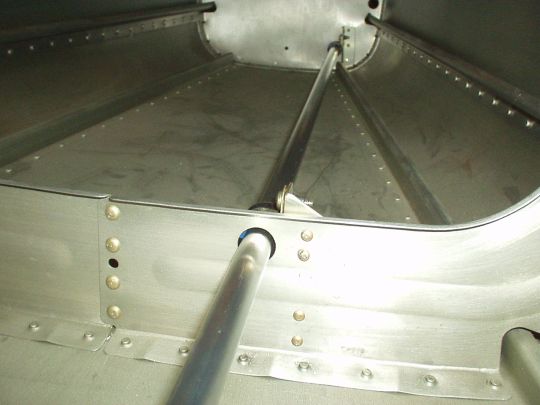
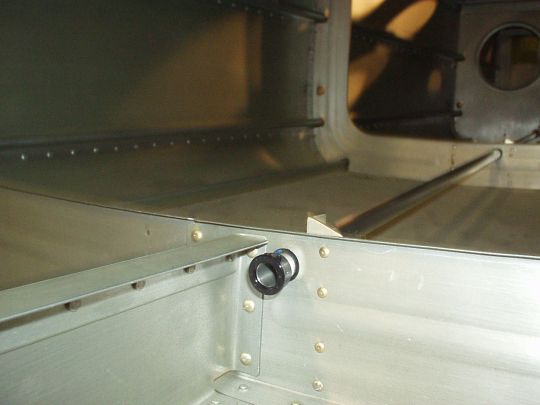
References